A bright idea ensures significant emission reductions
Process engineer David Edwards walked around the deck of the production ship Alvheim when a good idea sprung to his mind. Now this idea has been put into practice, saving the environment from significant emissions of greenhouse gases.
Greatly simplified, the solution consists of one pipe and two valves. And the result is that gas that would otherwise have been flared is instead sent by pipeline to the UK so that it can be utilized for house heating and boiling tea water (among many other things).
The challenge was linked to the well clean-up that must be done in new wells before they can enter regular production of oil and gas. There will be drilling mud and gravel in the well, and in addition the well will contain a special completion fluid which is necessary for the completion work. To wash this out, the well is run with as high flow rates as possible to a designated separator on deck. The gas from this process is vented out to the flare tower where it is burned.
Simple and ingenious solution
Some time back, process engineer David Edwards was walking on deck at the Alvheim FPSO. Then he sees the pipe that brings gas from the third-party separator to the flame tower. By turning his gaze slightly to the left, he sees the pipe system that brings gas from the producing well to the export pipeline.
“There and then I thought – what if we connect a pipe between the two systems so that we don’t have to burn valuable gas”, says Edwards.
The idea was quickly put into practice. Calculations showed that it was possible to implement, and if the manufacturing and installation happened at record speed, it could be ready for the start-up of the KEG (Kobra East Gekko) field, which was to be connected to Alvheim.
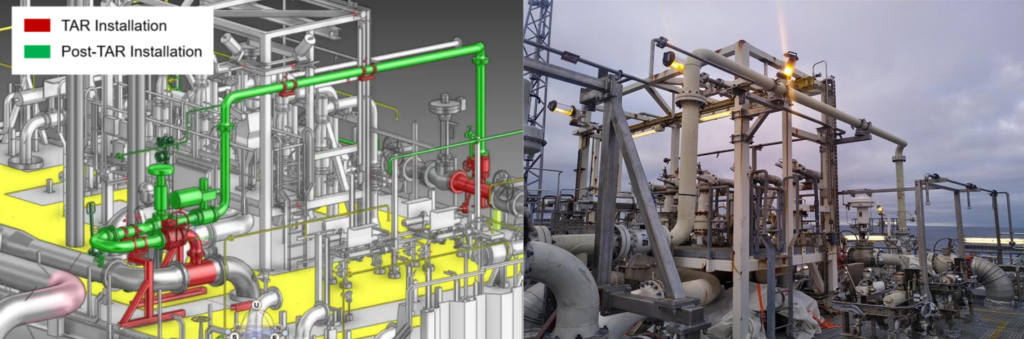
“We got the last parts for the system on board the week before KEG was to commence production, so there was no time to carry out test runs. So, you could say that the very first test was done when we put it into use”, says David Edwards.
“Then it is extra fun that the system turned out to work even a little better than the calculations suggested”, he says.
Significant emission cuts
With long multi-lateral wells, the clean-up process can last for several days. As a result, the amount of gas that is normally burned also becomes significant.
“We have now received real figures for the emission reduction from KEG. Although we have had some challenges with the compressors, they show that we have managed to extract 1 million cubic meters of gas, which would have resulted in CO2 emissions of 2,500 tons if we had flared it off, says David Edwards.
He also points out that the solution will be able to be used for future wells in the field, and that the experience and knowledge they are building up mean that a similar solution can perhaps also be installed in several fields.
“This is really what we can call a three-for-the-price-of-one”, says Edwards.
“We save the environment from emissions, save CO2 tax, and we get income from the gas we can sell.
Aker BP ASA is the Operator of Alvheim. Licensee is ConocoPhillips Skandinavia AS.
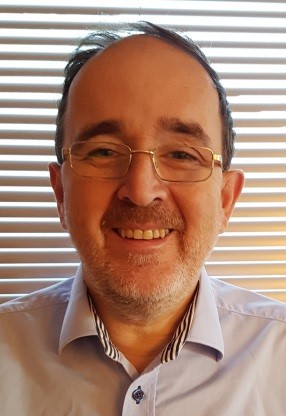